How does South Africa’s Mine Health and Safety Regulatory Instrument Fare in Managing Risks Associated with Mining
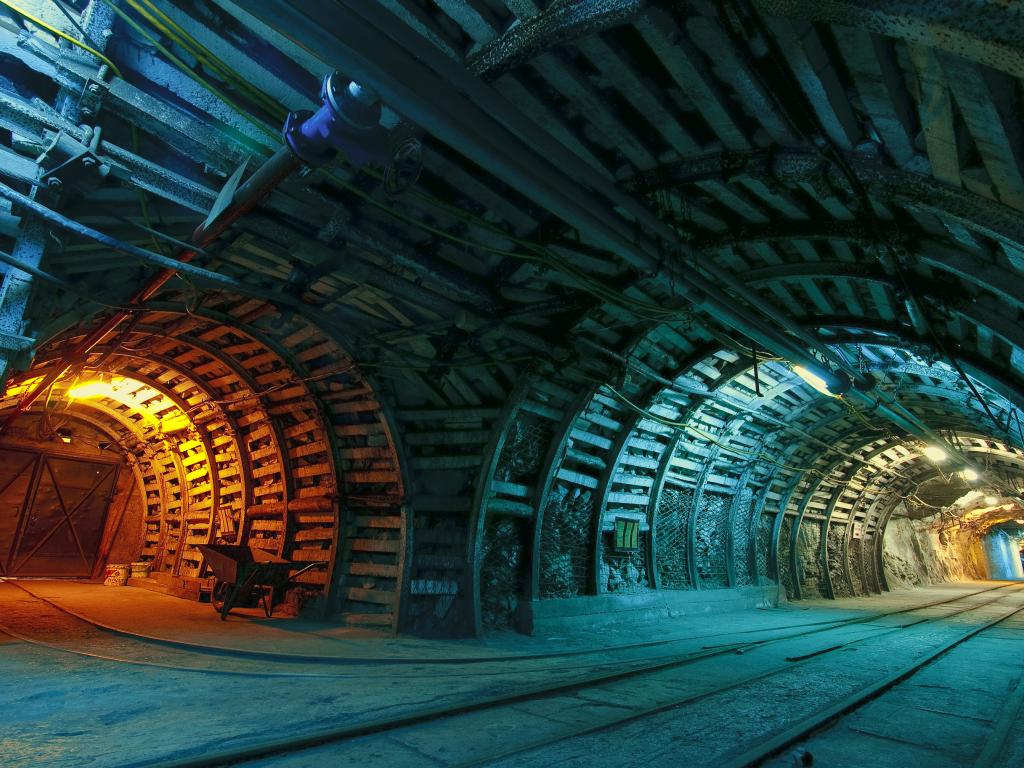
Introduction
South Africa has ratified the International Labour Organisation’s Convention on Safety and Health in Mines 176 of 1995 (ILO Convention 176). The ILO Convention 176 is the foremost international law instrument governing the regulation of health and safety in mines. The ratification of ILO Convention 176 commits South Africa to ensuring that it promulgates laws that implement health and safety measures that prevent fatalities, injuries or ill health affecting mine workers or communities that host mine operations. Furthermore, such commitment extends to implementing measures that mitigate health and safety hazards and risks in the mining industry.
Prudence and diligence are cardinals in mine health and safety regulation, particularly in a large-scale mining jurisdiction such as South Africa, where mine related accidents, injuries and deaths are unfortunate common occurrences. Renowned examples of these include the Lily Mine collapse disaster and the Impala Platinum Mine cage-lift accident. In 2024, South Africa recorded a cumulative 16% decrease in serious injuries in mines, in comparison to reported serious injuries in 2023. The decrease over a ten-year period sits at 41%.
Thus, it is imperative to critically assess South Africa’s implementation of the ILO’s Convention 176. ILO Convention 176 has nine principal aspects of mine health and safety, namely; the management of risks, measures eliminating risk, emergency response plans, dealing with physical, chemical and biological hazards, systems and training, health surveillance, employee rights, employee duties, as well as the laws and regulations encouraging the employee’s cooperation. This blog will focus on the management of risks.
The Measuring Yardstick: ILO Convention 176’s Requirement for Employers to Manage Risks Associated to Mining Operations
Article 6 of the ILO Convention on Safety and Health in Mines 176 of 1995, places an obligation on employers to articulate precisely on how they plan on managing risks associated with mining operations. The Article requires employers to deal with risks in the following manner.
- Step one, employers are required to eliminate the risk itself.
- Step two, where it is not possible to eliminate the risk itself, employers are then required to control and manage the risk at its originating source.
- Step three, employers are thereafter required to minimize the risk by way of designing safe work systems.
- Step four, employers are then required to provide personal protective equipment, for as long as the risk remains after steps one, two and three have been effected. It is important to note that the ILO Convention assesses these risk mitigation measures, against a ‘reasonable practicable and feasible’ standard, of which is not outlined by the ILO Convention itself.
South Africa’s Regulatory Response
The bespoke mine health and safety regulatory instrument in South Africa is the Mine Health and Safety Act 29 of 1996 (‘MHSA’). Section 2 of the MHSA, as a starting point, specifies that the employer is obligated to ensure a safe mine design, operation, maintenance, data collection, and reporting. The foremost obligation insofar as managing risks associated with mining is that of safe mine design. Under this specific obligation, the employer is obligated to ensure that the mine is designed, constructed and adequately equipped, so as to not expose employees and other persons to unhealthy and dangerous conditions. The standard of care expected from the employer, is that of ‘reasonable practicability’. The criterion for assessing ‘reasonable practicability’ considers; the severity and scope of the specified hazard or risk; the state of knowledge reasonably made available concerning such hazard or risk, as well as any means of removing or mitigating such risk.
The other obligations encapsulated within the prism of Section 2, are spread out across three sections under Chapter 2 of the MHSA, dealing with ‘Health and Safety at Mines’.
- The first is Section 6. Section 6 obligates employers to supply all the necessary health and safety equipment, such as personal protective equipment, to all employees.
- The second is Section 10. Section 10 obligates employers to provide adequate health and safety training to deal with risk associated with employees’ line of work. As outlined above, the standard is that of ‘reasonable practicability’. The purpose of Section 10 is to ensure that employees are well capacitated to deal with risk threatening employees’ health or safety.
- The third is Section 11. Section 11(1) obligates employers to adopt measures to; identify risks, then assess the identified risks; then record the significant hazards that have been identified and the assessed risks; as well as make the records of these identified hazards and assessed risks available to employees to peruse. Section 11(2) further obligates employers to effect measures that will; eliminate such recorded risks, controlling and managing the risk at its originating source; minimising the risk, and in the event where such risk subsists, to provide workers with personal protective equipment, as well as put in place systems with the capability of monitoring risks which employees may be exposed to.
Key Takeaways
South Africa’s current mine health and safety principal regulatory instrument, the MHSA, does well in eliminating risks associated with mining, as it requires employers to adopt risk identification measures at the originating source, or where not possible, risk management and mitigation, by way of the provision of personal protective equipment and training of mine workers.